Onsite Pediatric Earmold Fabrication
Ariadne - Ethan Zhou (CEO), Kayla Vallecillo (CTO), Erica Dong (CIO), Armaan Priyadarshan (CMO)
Problem Statement
The earmold manufacturing process is unnecessarily convoluted, lengthy, and expensive, which can be inconvenient for patients who use hearing aids. This issue is especially severe for pediatric patients, whose rapid development lead to frequent earmold refittings. A poorly-fit earmold can cause severe discomfort for the patient, hindering social and mental development in children.
Design Approach
To address the problem, our project proposes a process to enable fast and convenient fabrication of custom earmolds on the hospital site itself, allowing pediatric patients to receive new earmolds in a much more timely manner. This process involves taking a custom ear impression of the patient, scanning and processing this ear impression into a box cast designed for casting an earmold, 3D-printing the box cast, injecting the box cast with silicone, and finally fitting the patient with the produced earmold.
Prototype
The final design is the following earmold fabrication process (our project centered around creating a process, not a specific prototype):
- Take an ear impression from the patient and let it cure.
- Scan the ear impression, post-process the scan with the digital scanner’s accompanying software, and export it as an STL.
- Import the ear impression scan and design the earmold box cast with Cyfex Secret Ear Designer and a mesh manipulation software such as Autodesk Fusion.
- Print the box cast with a 3D printer of any type.
- Put together the box cast, prepare the silicone for injection, and prepare the pressure pot.
- Inject the silicone into the box cast and let cure.
- Remove the earmold and test for patient comfort.
Below are images for the two parts of a box cast (left), an example of a silicone earmold produced from the box cast (middle), and the silicone earmold fitted into the patient's ear (right).
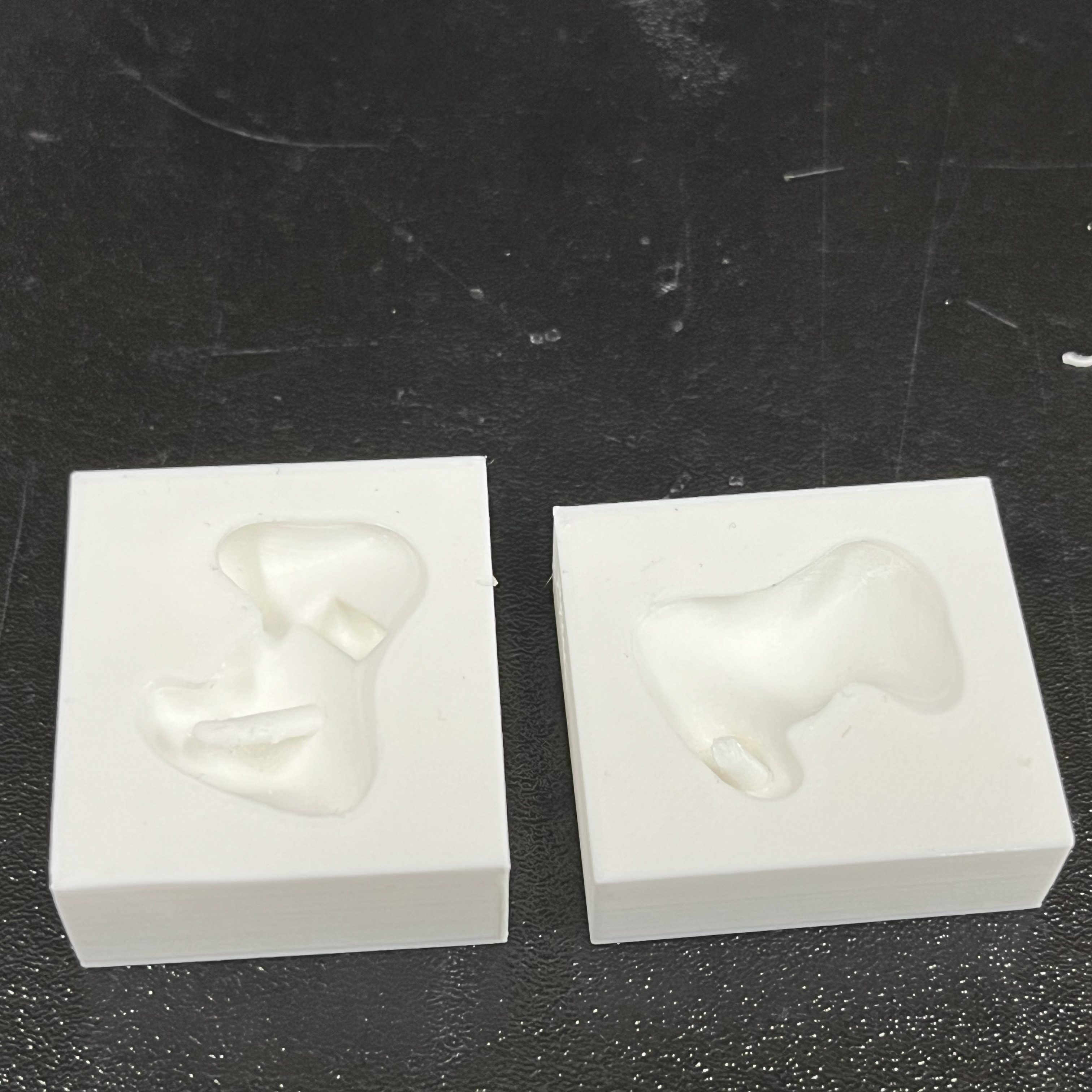
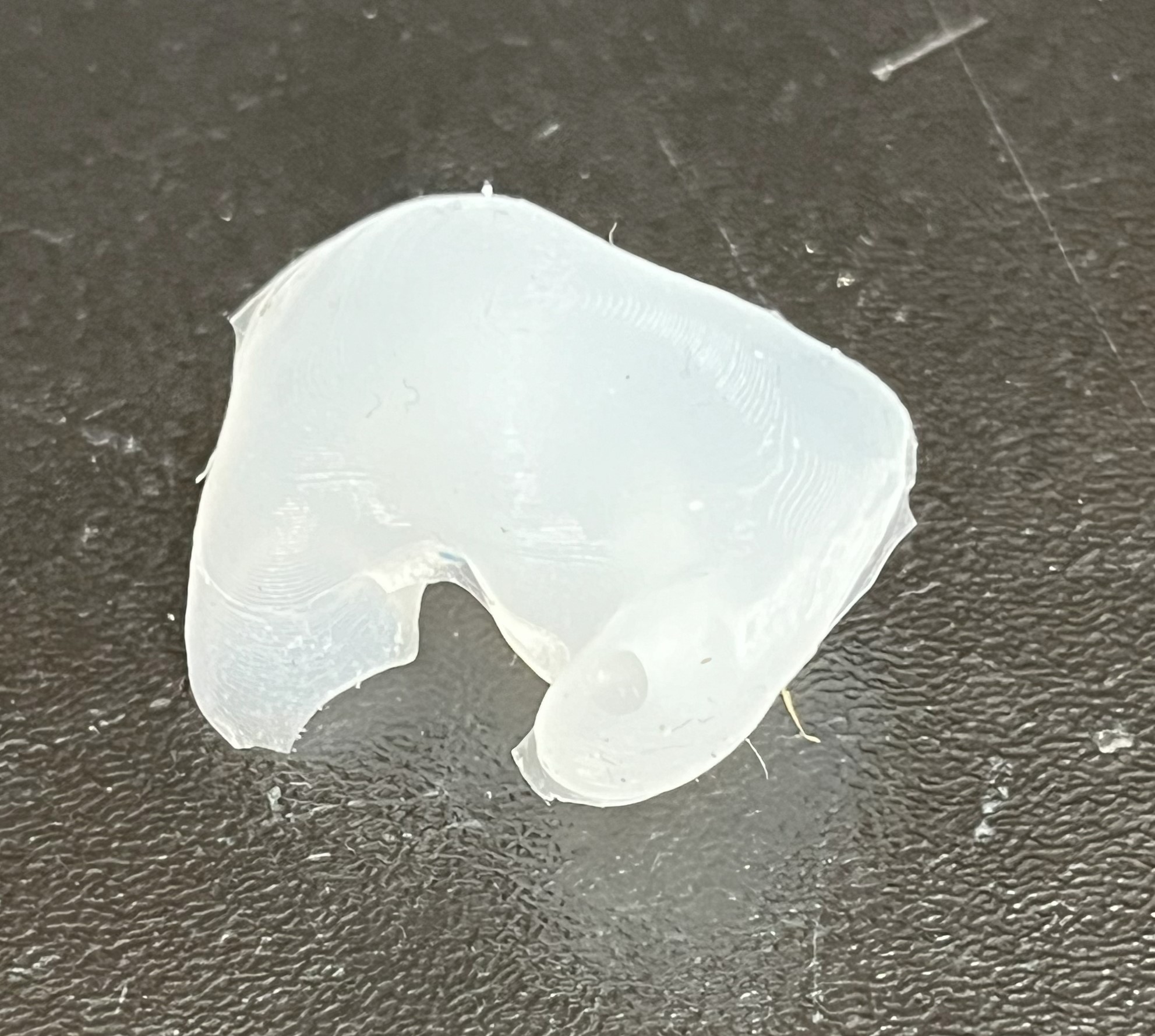
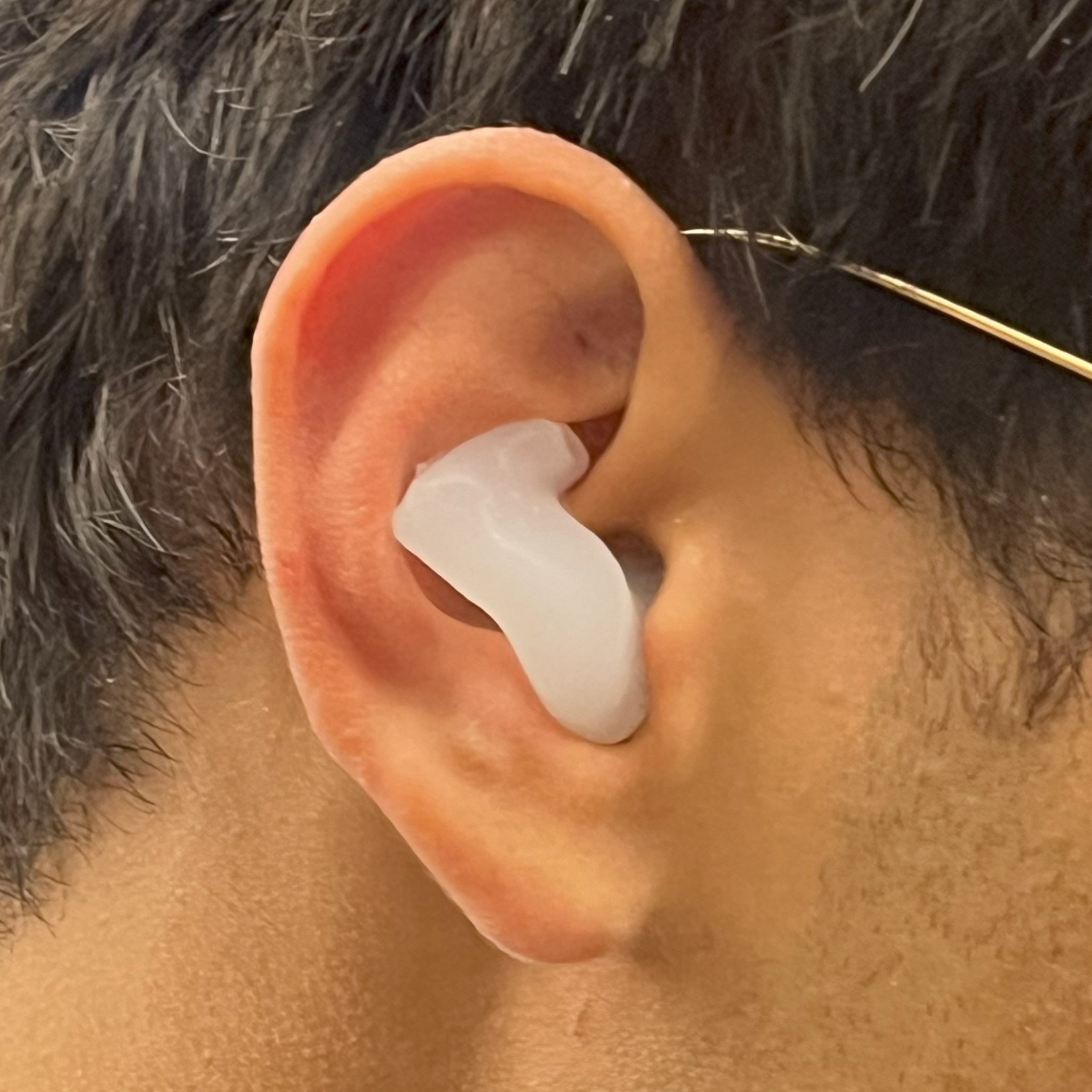
Prototype Fulfillment of Requirements
Overall, the design is very effective in fulfilling our Level 1 requirements as well as most Level 2 and 3 requirements.
Regarding Level 1 requirements, the final earmold is well-fitting and comfortable, soft and safe for skin, and does not cost too much to manufacture. The process also does not take too much space, making an onsite fabrication system at a hospital feasible.
Regarding Level 2 requirements, the earmold is durable and the process is not too convoluted, mainly consisting of taking impressions, operating various hardware and software tools, and making casts. Hence, this process is not difficult to learn. Unfortunately, the final cost of the system, at around $17,800, significantly exceeds the target cost of $5,000. However, most hospitals should still be able to afford such a system, especially considering the increased convenience and elimination of the middleman, and due to common medical devices frequently being even more expensive.
Regarding Level 3 requirements, a detailed instructions manual for setting up and maintaining the system was created. Although the time limit of 5 hours for a new earmold was not reached, the estimated time of 5.67 hours is very close to this limit, and remains much lower than the weeks that the conventional earmold refitting process would take.
Poster